Recipe Creation
Recipes are set up in BrewMan for each process/stage of production. Each recipe represents a process of the physical actions you do. E.g. For a brewery this may be a beer fermentation process, beer wort process or beer conditioning process of a specific liquid you produce. This then leads to the packaging recipe that you are putting this liquid into. E.g. 9G racking, 500ml bottles and 12x440ml Cases etc. Each recipe will then be tied together via a Batch Template. For a distillery, this could be separated into Distillation, Dilution, Blending etc.
To create recipes go to Production → Recipes → Create New Recipe.
Name - The name of this particular process you are creating i.e. IPA wort 1500L
Notes - Any recipe notes you want to add
Planned Duration Days - How many days this process traditionally takes. This is used for vessel scheduling to assist in vessel allocation.
Item Produced - What this process will produce at the end, this could be a product (IPA 50L Keg) or a material (IPA Wort). If you have not yet created bulk liquid materials or products you will need to do so.
Quantity Produced - How many/much of this item is produced typically i.e. 1x Keg or 1000x Litres
Scale By - When scaling this recipe would you like the recipe to be scaled by:
Volume - This will take the volume of produced items and used ingredients (unless specified as fixed qty) and scale them accordingly. For example if a Brew required 1000L of water and produced 1000L of beer scaling this by 2 will add a single instance of the recipe requiring 2000L of water and producing 2000L of beer.
Instances added - This will add as many instances of the recipe to a batch as specified. For example scaling a recipe for wort by 2x will mean that the the batch will contain 2 processes; Wort1 and Wort2
Press Save
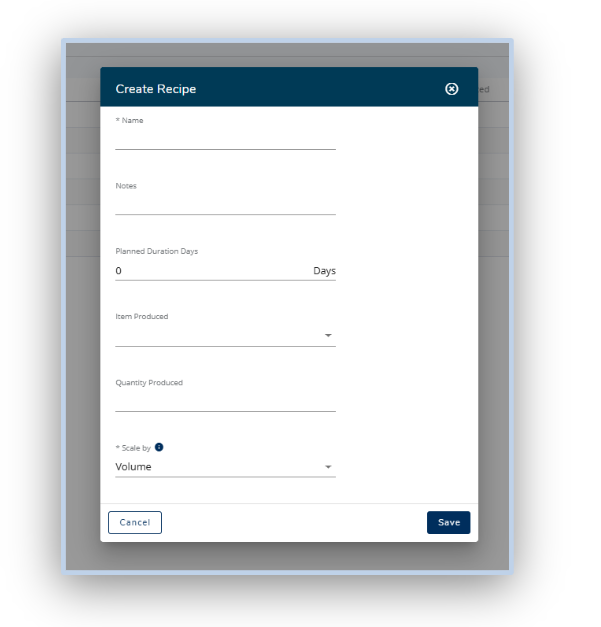
You will now be able to enter in as much information as you need for your recipe to prepopulate when creating a batch.
Ingredients - This will be any material you use in the stated process to complete this stage. Items such as hops, yeast and malt etc.
Fixed Quantity - Setting an ingredient to have a fixed quantity means that it will not scale if the recipe scales. If I had an ingredient of “Energy” and I chose to do a double batch, the Expected Qty of the Energy would remain the same.
Expected Qty - This is the amount of the ingredient that is typically used for this process, you will be able to dictate how much was actually used whilst in a batch.
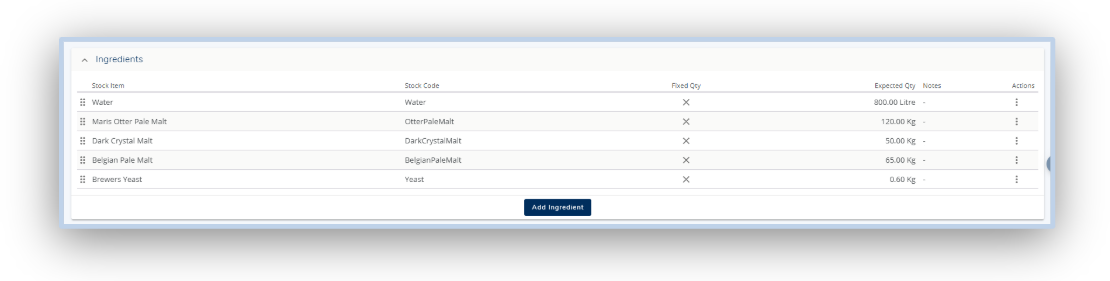
Instructions - Text boxes to apply any instructions for users to follow and mark off as completed during the process. These can be rearranged by clicking and dragging via the 6x dots on the left.
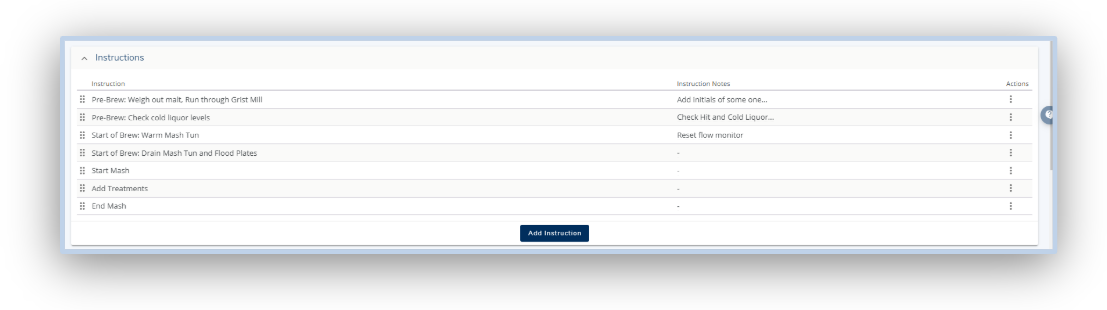
Vessel Requirements - The vessel capability and required capacity needed for this recipe, this will be used for vessel scheduling and also for prioritising vessels to the top of the list when selecting from a dropdown. Setting up vessel capabilities can be found HERE
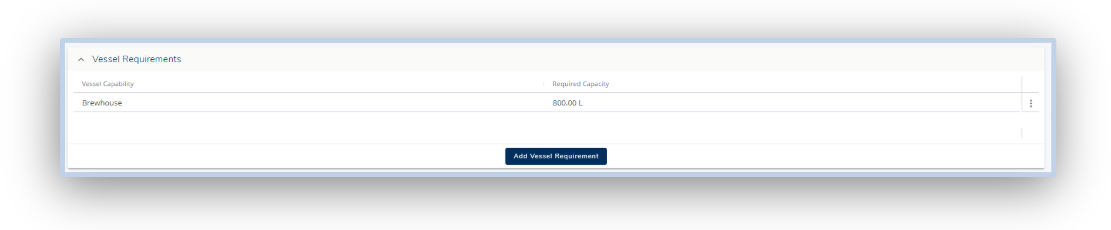
Quality Control Tests - Any QC tests that are needing to be recorded for this process. Once QC tests have been added to a recipe, select the 3x dots on the right and select “Edit Expectations”. For more information on blocking production outputs please click HERE.
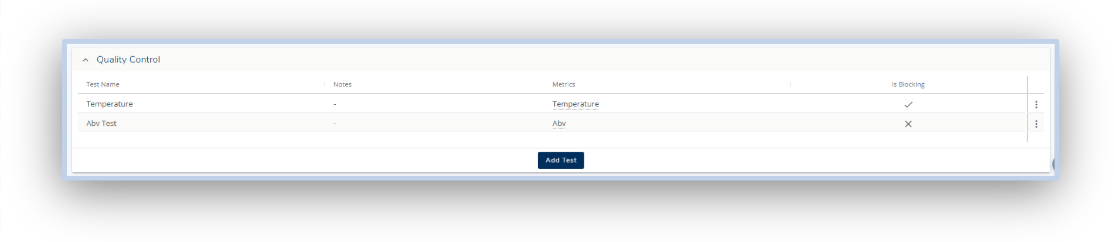
Batch Template Creation:
Batch Templates - This is a grouping mechanism for recipes tied to creating a certain liquid. You will need to enter a name, the item it produces and the fill colour of the vessel.
Recipes - Adding any recipes that are used to create this batch template. For example to make bulk beer; I need to add my recipes for the wort, the ferment and conditioning processes.
Was this helpful?
Comments
You must be logged in to comment in this article.
Login to comment